How to Improve Material Handling in Your Warehouse
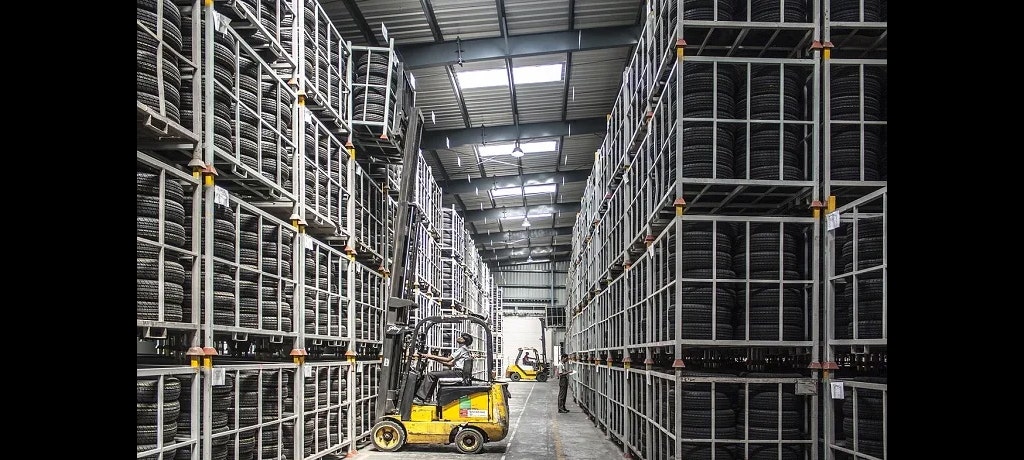
Owing to the intense competition in the third-party logistics (3PL) industry, warehouses and Distribution Centers (DC) are often forced to work on slim margins. Further, the ever-increasing fuel and labor costs eat into those thin margins, often resulting in negligible profits or even losses. As a result, they need to allocate more time and money in developing innovative technologies and processes to improve their productivity.
Material handling is one area that can increase the overall productivity and profitability dramatically, particularly inside the warehouse. Unfortunately, this aspect of a supply chain often remains overlooked. Let’s not dig deeper into the reasons behind this neglect. Instead, let’s focus on how you can improve material handling inside a warehouse and boost your profits.
Here are four tips that will prove helpful in this regard.
1) Provide Workers with the Right Material Handling Equipment
It may seem obvious, but using the right material handling equipment your time, storage space, and labor costs. It can also improve the workplace safety for your warehouse staff. Fortunately, you can choose from a variety of automated, semi-automated and manual equipment, depending on your application and budget. There are four basic types of equipment.
A) Storage and Handling Equipment
You can use storage and handling equipment to store and retrieve goods. Having the right one can maximize your storage efficiency, resulting in higher productivity. Common tools include pallet racks, drive-through or drive-in racks, sliding racks, stacking frames, shelves, bins and drawers, and mezzanines.
B) Automated Systems
Automated systems include advanced engineering systems such as Automated Storage and Retrieval Systems (AS/RS), Robotic delivery systems, Conveyor systems, and Automatic Guided Vehicles (AGV). These systems use a variety of technologies including robotics, Artificial Intelligence (AI), and laser sensors. All these systems can help you store, retrieve, and transport goods around the warehouse with maximum efficiency.
C) Bulk Handling
Bulk handling equipment includes conveyor belts, stackers (similar to forklifts), reclaimers, bucket elevators, and grain elevators. While receivers can recover bulk materials from a stockpile, stackers help to lift and stack heavy loads. Bucket elevators can haul bulk materials vertically, and grain elevators can move grains or similar goods from one place to other.
D) Transportation Equipment
Transportation equipment primarily consists of different types of industrial trucks that help move goods around in a warehouse. Examples of these trucks include hand trucks, pallet jacks, pallet trucks, walkie stackers, platform trucks, order pickers, side loaders, and AGVs.
2) Plan the Warehouse Layout
Plan the layout of the entire warehouse to increase your work efficiency and minimize safety hazards. You need to analyze the material flow, amount of incoming and outgoing traffic, seasonal inventory variations, and specific storage requirements. Be sure to eliminate any areas of high traffic or potential for cross-flow crashes.
You will need to define the following areas clearly:
- Loading and Unloading Areas
- Reception or Workstation Area
- Storage Area
- Picking Area
- Dispatch Area
Use these areas for their designated purpose only. For example, the storage area should only be used to store goods. Don’t use it to park forklifts or any other equipment. You should also be able to retrieve one product without the need to move to another. Make sure to organize the items in the storage area depending on accessibility.
For instance, storing frequently picked items in the front can save travel time within the warehouse, resulting in higher efficiency. You should also organize your storage racks in rows with enough space between them to move the forklifts and weight carrying machines around.
3) Train Your Warehouse Staff
With all the heavy equipment and goods moving around constantly, a warehouse becomes one of the most dangerous workplaces out there. According to the Bureau of Labor Statistics (BLS), in the warehousing and storage industry, the average rate of injury and illness cases per 100 full-time workers was 5 in 2017 with a total of 22 recorded fatalities.
It is necessary to be aware of the potential dangers for safety as well as financial reasons. Workplace injuries can lead to heavy worker’s compensations putting more stress on your finances. Regular training can improve the safety and productivity of your warehouse. Make sure to provide training to employees who operate heavy equipment such as industrial trucks, forklifts, material handling systems, and lifting cranes.
Only a qualified person should provide training that involves both, formal instructions and practical demonstrations. Teach them about various controls, instruments, and steering and maneuvering techniques. For manual handling, teach your employees to avoid potentially hazardous actions such as unnecessary bending or twisting, jerky movements, and lifting excessive weights.
4) Improve Forecast Accuracy
Forecasting plays a critical role in warehouse management. Inaccurate forecasts often lead to excess inventory, which in turn, reduces storage efficiency and increases warehousing costs. Further, seasonal fluctuations and ever-changing consumer demand also make it necessary to have a sophisticated inventory forecast system in place.
If you still rely on manual inventory management using spreadsheets and paper documents, it is time to upgrade to a software-based solution. You should invest in a Warehouse Management System (WMS).
It will allow you to anticipate your future inventory in real-time. You can determine projected shipping dates for fulfilling customer orders, see the seasonal demand variations, and set timeframes and preferred stock levels with just a click.
However, with a large number of internal and external inventory management factors involved, chances of data misinterpretation and distortion are high. To avoid this inefficiency, make your forecasts at the customer level.
Also, filter out the items that are no longer available from the database to improve forecasting accuracy. Lastly, keep evaluating your forecasting accuracy to monitor your progress. Document the forecast data and use it for future reference.
Final Words
As you can see, it is possible to improve your material handling practices, resulting in increased warehouse productivity. From providing the right material handling equipment to improving inventory forecasting, none of these tips are difficult to implement. What steps did you take to improve material handling in your warehouse? Did you use any of the four steps mentioned here? Tell us more about your warehouse management efforts in your comments.
Shop Online